Earlier this year, Pierre Chaponnière, Application Engineer at YellowScan, talked about the benefits of Direct Georeferencing for simultaneous LiDAR / Photogrammetry versus Traditional Aerial Triangulation systems and exemplified its use with a case study of a quarry in France. This subject picks up on some of the information we discussed in an article around how to use a drone for aerial surveying instead of arguing about Photogrammetry vs LiDAR.
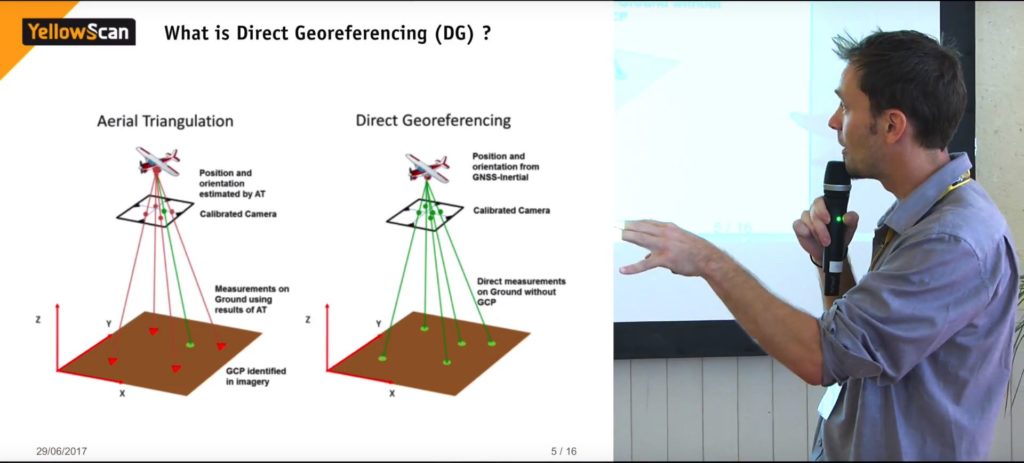
To start off the presentation, Pierre discussed a bit about the main differences between Aerial Triangulation and Direct Georeferencing. As Pierre puts it, “Aerial Triangulation (AT) is sort of an upward workflow”. Simply put, this process works through the identification of ground control points (GCP) or tie points on the collected images - this could be images or LiDAR point cloud - to position and orientate your platform, and then generate results, such as an orthophoto.
On the other hand, Direct Georeferencing (DG) consists in using high-grade IMUs - YellowScan mentioned the
Applanix APX 15 - resulting in “a
centidegree accuracy in rolling, pitching, and heading”. This means it’s possible to get the full accuracy of both the platform’s position and orientation, and accurately position each point of your LiDAR or photogrammetry pixel. “This gives you the ability to quickly georeference any points because you already georeferenced and you can just position your data”.
Putting it into practiceAfter introducing and comparing both methods, Pierre moved onto the case study of a 25 hectares (ha) quarry site, with a 140m deep pit and high steep walls, to the south of France. The case study consisted of collecting different data, such as quarterly maps, and volumetric calculations, by using three different survey methods on the same day, with the same weather conditions and hour slots. One of the methods was a Terrestrial LiDAR System (TLS) - a Trimble TX5 mounted on a tripod, which reaches a frequency of up to 976kHz, and has a range of up to 120m.
Then, there was the DJI Inspire, used as a photogrammetric sensor for the Traditional Aerial Triangulation system, equipped with a 16MP camera.
At the same time, YellowScan used its LiDAR scanner Surveyor equipped with the Applanix APX15 on a drone, mounted in a combo with a 24MP camera.
The set upSetting up a TLS isn’t an easy task. Initially, the network set up is rather tricky, as you need to set up a checkerboard in order to actually position your tripod and achieve an absolute positioning reference to the scanner. Then, you need to move around with a few reflective spheres to relay your station from one to the other. “So, there's a lot of movement and a lot of moving parts around in Terrestrial LiDAR scanning”, Pierre adds.
“Then, in terms of the DJI Inspire and the photogrammetry process, the operative constraints are fairly simple in terms of flight planning,” Pierre continued, “The only thing you need to do pre-flight, is just having a network of ground control points and targets in order to actually shoot them from the drone, and then being able to visualize them on your acquisition. So, this takes a bit of time and effort to deploy”.
In regards to the YellowScan Surveyor Combo, you only need a GNSS base station that works in PPK mode. This means you can be five kilometers away from it with the drone, and you'll still get good correction results. However, since the scanner has a limited range, you need to adapt your flying altitude to the terrain.
Timing and results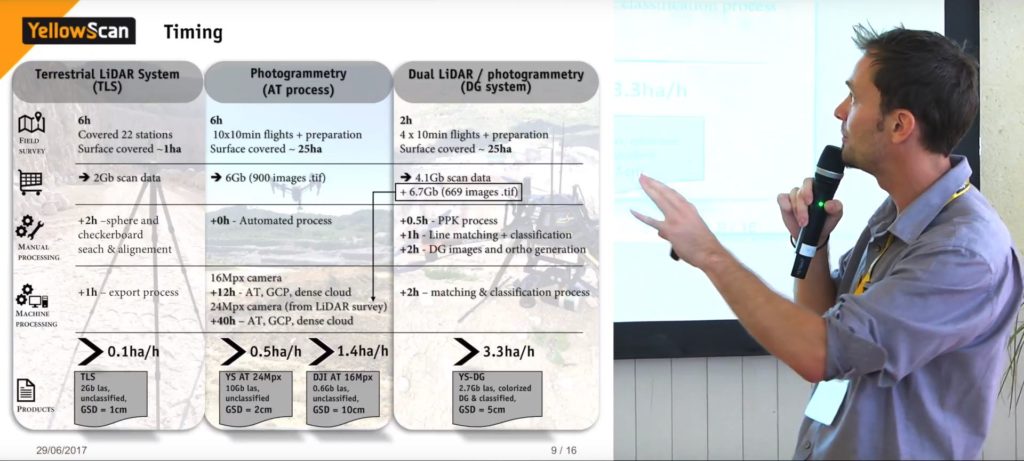
After calculating and placing each method’s results side by side, it becomes apparent where the real differences, advantages, and disadvantages are over each other.
In 6 hours, the TLS covered 22 stations, 1 hectare, and generated 2Gb of data, whereas the AT process with the DJI Inspire covered 25ha, took the same amount of time (with 10x10min flights and preparation), and generated 6Gb of data. However, due to the luminosity variations, the DJI Inspire needed two days to complete the process (3 hours each day in a specific time slot).
On top of that, the YellowScan Surveyor Combo, equipped with the DG system, managed to cover 25ha in 2 hours, with only 4x10min flights and preparation, as it only needed one passage over a specific part of the quarry to capture the necessary points. The result was 4.1Gb of data from the LiDAR scanner, and 6.7Gb from the 24MP camera.
Additionally, you need to take into account the amount of time of manual processing (where you need to intervene in the process to achieve the desired result), and machine processing (where you leave the computer to deal with the data alone).
So, the TLS took +3 hours to finish the process: +2 hours of moving spheres around and aligning checkerboards, and +1 hour in exporting the data to the computer.
The DJI Inspire didn’t take any time in the manual processing phase, since it is an automated process. However, it took +12 hours for the computer to process the Aerial Triangulation, detect GCPs and create a dense cloud. Furthermore, YellowScan also decided to perform the AT process for the 6.7Gb data captured from the high resolution 24MP camera, which ended up taking +40 hours.
Finally, the YellowScan Surveyor took +3.5h to perform the PPK process, classify and match lines, and process DG images as well as ortho generation. Additionally, the computer took +2h to perform the matching and classification process.
Coverage production rateIn the end, all of these steps translate to a single product from each process:
The TLS generates an unclassified 2Gb LAS file, with a Ground Sample Distance (GSD) of 1cm, meaning it has a production rate of 0.1ha/h;
The DJI Inspire 16MP camera AT process resulted in an unclassified 0.6Gb LAS file, with a GSD of 10cm, ending in a higher production rate of 1.4ha/h, while the YellowScan 24MP camera AT process finished with an unclassified 10Gb LAS file, with a GSD of 2cm, and a lower production rate of 0.5ha/h.
The dominant one here was the YellowScan Surveyor, which generated a classified 2.7Gb LAS file, with colorized DG, and a GSD of 5cm. The production rate was the highest one of the four, at 3.3ha/h.
Point-by-point vs Cloud-to-Cloud vs Section-to-Section accuracy assessment
To validate the acquired products and their accuracy when compared with the real world, YellowScan used the RMSE measure, as shown in the image above. On a point-by-point measurement (left-side image), the YellowScan Surveyor didn’t stand out when compared with the photogrammetric solutions.
However, when you move on to a wider area (image on the right), you start to see the differences between them. The image represents a parcel of ground with steep curves and slope changes. While the YellowScan Surveyor with the Direct Georeferencing system doesn’t show any errors, the
DJI Inspire produces a lot of artifacts when generating the model when it comes to “brutal slope changes”.
Pierre said: “The Aerial Triangulation process works well, but not really at slope changes, [as it] generates a lot of artifacts there”.
Moreover, Pierre also talked about vegetation penetration, as well as infrastructure mapping, and showed a comparison between the two - check images below.
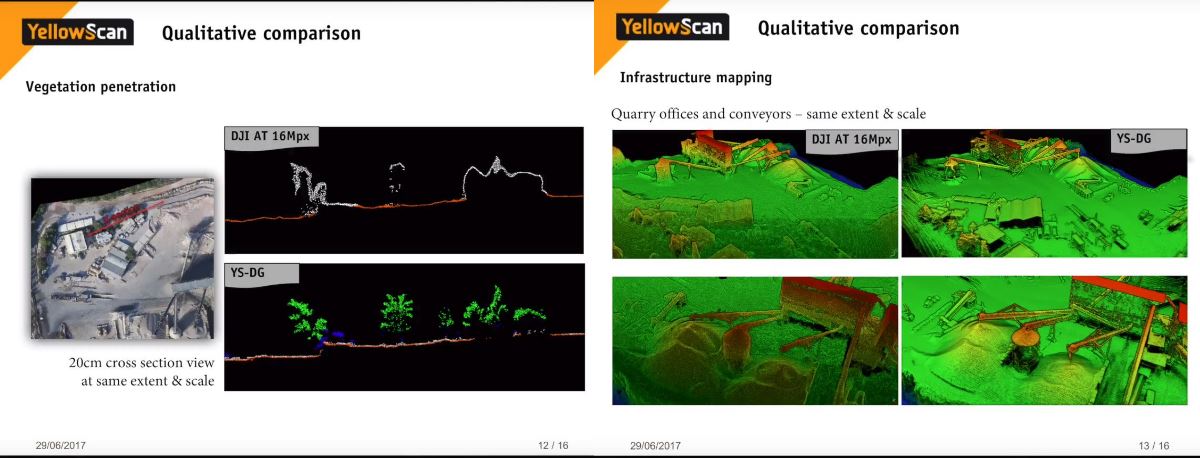
On the left side, although the YellowScan Surveyor leaves a few holes in denser vegetation areas, it does show a better representation of what it looks like than the DJI AT process. Then, on the right, you can see how much more detailed the infrastructure is on the YellowScan Surveyor example.
The conclusionTo wrap up the presentation, Pierre talked about the benefits of using a combo like the YellowScan Surveyor, with a 24 MP camera and the Direct Georeferencing system - in this case, the Applanix APX 15 - over an AT Photogrammetry solution.
To start with, the LiDAR/photo DG solution provides faster survey and processing times. Ground truth points or GCPs are not as critically needed as they would be in a AT photogrammetry process. The only point that needs to be well positioned is the landmark the base station is setup on, the rest would work rather as validation points for reporting and quality checks.
A single flight path of a LiDAR survey offers much wider coverage than photogrammetry, It isn’t affected by sunlight as opposed to AT photogrammetry which is light dependent; image correlation issues don’t impact the result; and it has the ability to capture fine infrastructures or objects, such as power lines, and conveyors.
Additionally and on a more general note, remote sensing surveys provide safer operations, no disturbance or operation downtime, as well as faster data collection and a wider field of view.
One of the questions we posed in
last year’s article was around whether or not photogrammetry was better than LiDAR, or vice-versa. The answer is that it all depends on what you want to do. However, YellowScan created a solution that combines both technologies, and by adding a Direct Georeferencing board to the mix, it ends up offering better results.
As YellowScan mentions in one of the slides of the presentation, the YellowScan Surveyor combo is “the one tool every surveyor needs”, and by combining the best of what photogrammetry and LiDAR have to offer, it’s hard to argue with that assessment.
Comments