It’s been a few weeks now since Commercial UAV Expo Europe took place in Amsterdam, and we've seen session and video highlights that showcase some of what happened. Before I went to the event, I published a blog that laid out five things I was watching out for at the Expo. It's time to take a look at how those expectations lined up with reality.
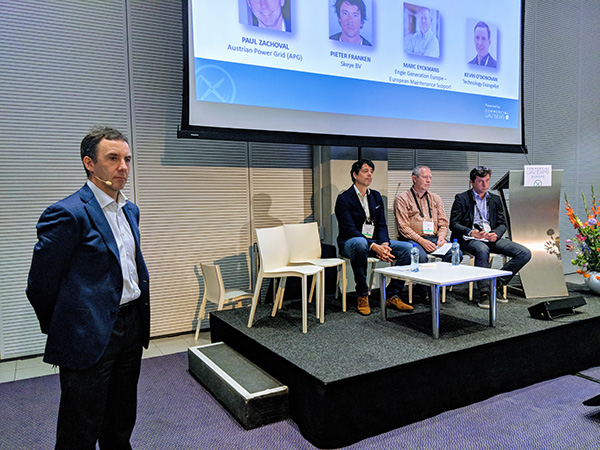
- More companies are establishing drone operations in-house as opposed to simply out-sourcing everything.
- There is a move away from full vertically integrated solutions being offered by drone service companies to a more targeted ‘best of breed’ solutions.
- As the Industry matures, many drone service companies shifting strategy to deliver a ‘platform’ for drone operations as opposed to an ad-hoc solution.
- EU Regulation is still very ‘painful’, varies widely between regions/countries and is evolving very very slowly. This is the Industry's greatest pain point.
- Machine learning algorithms are improving for specific use cases. ‘Supervised’ Machine Learning is the way forward for now. Artificial Intelligence (AI) based Drones are a long, long way away.
- Drone operations are becoming more automated, but Autonomous Drones are a long way off.
- Sensor payloads are expanding with bigger/better & new functionalities being added, especially when it comes to adding LIDAR.
- Don’t just think of drones in terms of what we see today – think about crawlers, robots, on water/underwater drones, high-altitude drones, low orbit inexpensive satellites …
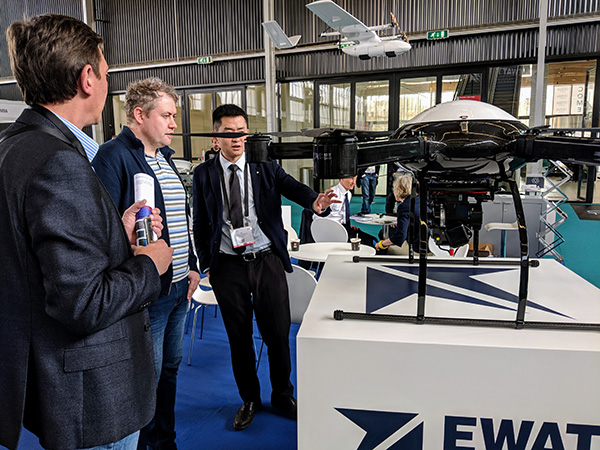
- i) Hight Altitude Drones – There was a great deal of talk about large, fixed-wing drones that can be deployed at high altitude, which can stay in position for weeks/months at a time and remain out of the way of commercial aircraft. Not surprisingly, it's something the biggest companies in the space are looking to figure out. Depending on the sensors they carry, you could use these types of drones to get almost real-time imaging of a complete Transmission Line, Pipeline or a facility. It would be always up there. Commercial versions of the Zephyr Airbus system would be an example. Imagine the possibilities…
- ii) Measuring Metal Fatigue - While the ability to detect signs of metal fatigue via image processing are advancing rapidly, Industry best practice today is to do physical contact based metal/structure testing to get accurate results for thickness & internal defects. So what RoNik Inspectioneering B.V. has developed is really innovative. Check out their video here:
Comments