One of the key value propositions originally made for drones was its capacity to gather large amounts of high-quality, high-resolution data faster, cheaper, and safer than manual data collection. However, early adopters quickly found out that once that data was collected, it still needed to be processed. For many, this usually meant manually combing through gigabytes of images to find a specific person or thing, requiring a significant amount of time and labor. So, whatever value that drones proposed to provide on data gathering was more than made up on data processing. This contributed to a slower adoption rate of drones in commercial industries than was originally predicted as companies drowned in data and were unable to obtain a return on their investment.
Commercial UAV News has often spoken about the challenges of processing big data sets collected via drone and the many ways the industry is working on solving that bottleneck in data processing. Most of these solutions involve, in some way, machine learning algorithms and computer vision. But training and developing a reliable and accurate machine learning algorithm from scratch is something that requires resources and expertise that most people are not able to allocate funds or personnel toward.
Automating Detections in Postprocessing
Yet, there has been significant growth in industries where machine learning has been developed reliably for drone applications, especially in industrial inspections, oil and gas, and search and rescue. The question is how can we accelerate and democratize this process for the specific needs of businesses who need a faster way to process large data sets? This is where companies like Teraki are revolutionizing machine learning for drone companies.
“There are two elements to our technology. First, we have a market leading way to reduce the data of any given sensor stream, and we have the ability to intelligently prefilter that information using machine learning,” explained Geert-Jan van Nunen, CCO of Teraki, to Commercial UAV News. “The great thing is that the customer defines what information is relevant and required. For example, a user can decide to use our software for crack detection. They can fly over a construction site, bridge, chimney, or any other industrial object to detect those cracks or any other anomaly and train our software to detect those cracks. This will not only enable you to transmit more efficiently to your website or cloud, but it will also enable you to basically skip the whole human part, where you go over hours of video marking up the video, which is tedious work.”
Processing begins as the drone is collecting the data using machine learning to identify key points of interest and marking them, removing the need to process the data once you are back from the field and manually go through unprocessed images and mark them up.
Teraki’s online software has streamlined the machine learning process by providing a user-friendly interface to help companies train their computers to detect specific regions or periods of time that are of interest. The process is simplified by Teraki so that all a user has to do to train the program is to upload images into the Teraki platform and mark what needs to be detected. As more images are uploaded, the more accurate the detection gets.

Example screenshot of Teraki Platform
“If I am not an AI expert or I don’t have a data scientist working in my company, which is probably most often the case, Teraki’s user interface is very intuitive,” stated van Nunen as he walked through the process. “Any new project goes through these steps: you upload the data from your drone particularly the ones that contain relevant information, you label it, you validate the model, and then you’ve trained it. The first run, depending on the volume of data, should have decent accuracy—90% to 95% accuracy. Then you keep adding data and videos and the accuracy rates can go up to 99% and further. You don’t need to do the data analysis or be a data scientist yourself to utilize our software.”
Essentially, by doing what most people are doing manually already—marking up images and identifying specific regions or times of interest—companies can introduce machine learning efficiencies into their workflows.
Enabling More Applications to Run on a Drone
Teraki takes machine learning one step further by putting that processing power on the drone to efficiently process data on the edge, while the drone is in flight.
“You may ask if this is only an AI pipeline training tool, but it is for sure more than that because it also directly deploys these machine learning models to your drones,” van Nunen added. “You upload the model, and your drones will be immediately running the machine learning model directly out in the field.”
This is called smart edge data processing and it is set to open up the drone industry in new and exciting ways by addressing some major roadblocks in data processing while also improving drone performance.
Enabling smart edge processing is proving to be very important for the evolution of machine learning. This is because even as we gain traction with machine learning capabilities other issues are presenting themselves that require a more streamlined approach to data processing, such as the need for online workflows; near real-time data transfer of information, especially over connected devices; and battery/fuel/processing efficiency. This is where edge computing is able to provide additional benefits to machine learning.
What is edge processing? For drones, this is the processing of a data signal in the drone, most likely coming from a sensor like a camera, lidar, and other kinds of telematics, to produce information about that data. This is done before it is sent out to the cloud or other storage device, but the pre-processed information can also be used directly in the drone (e.g. for avoiding objects, autonomy, etc.). A smart edge process intelligently weeds through the incoming data signal to find the data that is important to the mission and then filters out unneeded information in order to maximize network bandwidth and processing efficiency and lessen demands on the CPU (central processing unit).
In essence this is making the CPU more efficient (by about a factor of 10), as it frees up computing power. So, this either means that the bill of material of the drone can be lowered—making for lower costs; or the current CPU can process more applications at the same time and energy. In particular, the latter option enables you to collect more information.
Lessening the demand on the CPU has some positive consequences in terms of hardware cost, time, and energy efficiency. In terms of cost, lowering the demand on the CPU means that a drone can operate at a high level without requiring an expensive chipset. In terms of energy efficiency, less processing means less drain on the battery and a lighter CPU unit; both of which add time to your flight and the life of your drone. In terms of time, processing begins as the drone is collecting the data using machine learning to identify key points of interest and packaging that information into useable data. This is in stark contrast to manual data processing methods where you have to process the data once you are back from the field manually going through unprocessed images and marking them up.
“You are able to host more applications in the drone at higher resolution because you do not need to process, say, 100,000 data points per frame, but only 10,000 data points per frame. The freed up processing power can be used to run additional applications or to process higher resolution images,” stated van Nunen, explaining the value add further. “For example, next to a crack inspection you can host a crop inspection application in the drone as well.”
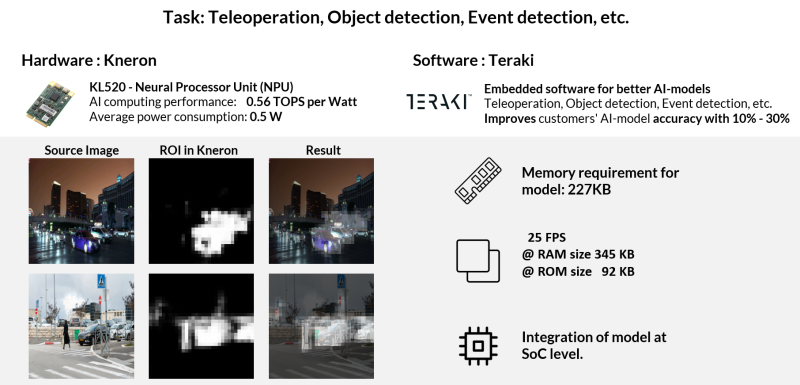
Example of highly cost-effective; highly energy efficient chipset (from Kneron) that can run Teraki’s software.
Teraki’s software platform weeds out the data you don’t need (such as wide swaths of blue sky) to make the drone CPU more efficient and save costs and energy, while providing a higher accuracy model that detects things like cracks along a chimney stack, people in a search and rescue mission, or objects for avoid applications.
Essentially, anyone who has to process large chunks of sensor data coming from their drone or wants to run more applications within the given computing resources in the drone can utilize Teraki’s software, which is subscription based, to streamline their processes and workflows.
To learn more about Teraki, check out their latest webinar on Commercial UAV News here.
Comments