In developing high-performance drones for a wide range of applications, the AIR6 SYSTEMS team has created significant value in multiple industries. Between their AIR8 Medium Lifter, AIR4 Rugged, AIR4 LIGHT and AIR4 NANO, operators have a variety of choices to perform manual and automated flights, enabling more efficient and safer inspections, surveys, monitoring and more. A recent webinar showcased how this value can be taken to the next level thanks to their development of a new drone simulation platform.
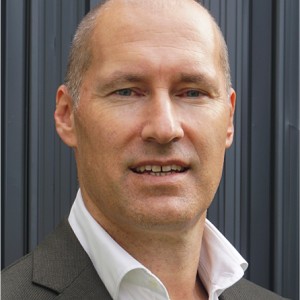
The AirborneSIM is a state-of-the-art drone simulation platform designed to revolutionize UAV operations. It can replicate high-risk missions without having to step foot into the field, allowing users to effectively mitigate risks while also testing BVLOS operations, ensuring compliance and safety. Alex Fraess-Ehrfeld, founder & CEO of AIR6 Systems, spoke on the webinar and explained why simulation could be a game-changer for drone operations, but we wanted to learn more. See what he has to say about how clients are using these systems, what kind of a difference simulation can make, how such capabilities can impact planning for BVLOS operations and much more.
Jeremiah Karpowicz: We've previously explored exactly what "drone autonomy" does (and doesn't) mean, but how are you using that term in 2025? Have recent innovations changed how you talk about and utilize autonomous drones?
Alex Fraess-Ehrfeld: What I stated in 2022 about autonomy remains valid; however, we have since made significant progress in realizing "end-to-end" (full) autonomy. This leap forward is partly due to advancements in drone and sensor technology and partly because we had developed more sophisticated tools, such as advanced navigation AI and robust simulation frameworks.
Ultimately, whether partial or full, autonomy is designed to make a pilot’s life easier. While humans will remain in the loop for the foreseeable future, overall systems are becoming increasingly efficient, safer, and more predictable. For now, autonomy primarily supports pilots by enhancing their ability to perform tasks, making successful missions less reliant on individual flying skills. This principle has been applied for over a decade, particularly in mission planning software and automated flying, which have become standard in surveying missions. In inspection tasks—such as examining buildings or steel structures—autonomy becomes even more critical. Approaching such structures manually navigated, especially in GPS-denied environments, would often be impossible without vision-based AI to guide the process.
At AIR6 Systems, we emphasize the distinction between research and development (R&D) efforts and market-ready products. Looking ahead to 2025 and beyond, our primary R&D focus lies in BVLOS autonomy. This involves situations where the pilot’s location differs from the drone’s start and landing points, whether operating from a fixed installation or a mobile platform, such as a trailer or vessel. In these contexts, (semi-)autonomy will play a pivotal role. In the future, even path-planning in such operations will leverage AI to adjust for risks and comply with airspace restrictions.
Your solutions are being utilized for inspection purposes in a variety of sectors, but generally speaking, how are your clients measuring the value of these applications? Is it in terms of performing an established task in a faster, cheaper or safer way? Or by using your technology to do something that they couldn't have done with any other tool?
Our drones are utilized for a variety of tasks, including inspections, monitoring, surveying, and logistics. With these solutions, we address specific, real-world needs or challenges, often brought to us by customers or end-users. These are problems that cannot be effectively solved without drones or the information they provide.
Moreover, as you mentioned, drones enable tasks to be completed faster, more cost-effectively, and with greater safety. For improvements to existing methods to be viable as a business model, they must deliver substantial advantages. For example, we remain sceptical about AAM (Advanced Air Mobility) or air taxis that fail to show clear, significant benefits over helicopters. Without such advantages, we don’t see a sustainable business model in that space. However, we strongly believe in last- and mid-mile logistics for high-value items and medical emergencies.
One example of our solutions is a drone designed for pipe inspections. This innovative system enables a drone to land on steel pipes and deploy a magnetic crawler that travels along and around the pipes to measure wall thickness. Traditionally, this task would require a crew of engineers, the construction of costly scaffolding, and extensive time. The inspection would often take weeks or months, during which the pipe section would be out of service. By contrast, our drone solution eliminates the need for scaffolding, allowing an engineer to manage the entire process from the ground—delivering significant savings in time, cost, and safety.
Similarly, our DrSOLAR solution revolutionizes solar panel inspections using SWIR sensors and electroluminescence technology. With this approach, solar PV O&M teams can quickly and accurately detect faults and even microscopic hairline cracks in solar panels. Compared to traditional methods, this solution offers considerable improvements in time, cost, and safety. Additionally, it provides distinct advantages over drone-based thermography, enabling more precise and comprehensive inspections, showing the real power production loss of each fault.
You were part of a recent webinar that fully explored AirborneSIM, your new drone simulation platform designed to revolutionize UAV operations. What kind of a difference can this kind of simulation make to operators and teams?
Simulation has become a critical component of our strategy and a powerful tool for our customers. Originally developed for R&D purposes in offshore wind turbine inspections, simulation addressed the challenges of accessing offshore wind parks due to costs, weather conditions, and permissions. We needed a tool for technical desktop development, to showcase our processes to stakeholders, and to conduct as much testing as possible in a digital environment before executing a single real-world attempt. To achieve this, we began building a highly realistic technical digital twin of our drones within a high-fidelity simulation environment.
It quickly became evident that simulation is far more than just a tool for technical development and demonstrations. In an era of increasingly complex scenarios and heightened requirements for risk mitigation—particularly for BVLOS operations—simulation has proven to be an indispensable resource for operational planning, testing, and validation.
Additionally, as a valuable side benefit, our simulation platform serves multiple other purposes. It can be used for pilot training, whether for manual flying or automated missions, and as a 3D demonstration and risk assessment tool for regulators. These capabilities make simulation not just a tool for development but also a cornerstone for operational safety and efficiency.
Are there any specific ways that the Mission Planning & Validation capabilities are different or distinct from other options available in the market?
Yes, we believe AirborneSIM is a completely unique solution, unlike anything currently available on the market. It provides an accurate digital twin of our drones, incorporating all design characteristics—physics, sensors, subsystems, and functionalities. Users can practice and test their mission planning in a realistic 3D synthetic environment while also improving their manual flying skills.
As a fully software-based tool, AirborneSIM can be easily installed on the customer’s PC. It seamlessly integrates with widely used flight planning tools such as QGroundControl and MissionPlanner. This allows users to plan missions using their preferred flight planning software, upload them to the simulator, and perform testing, validation, and adjustments within a highly realistic simulation environment. Users can simulate flights in their hometown or anywhere in the world—be it Miami, London, Rome, or any location they choose.
With AirborneSIM at your desk for just a few weeks—connected to your RC controller—I guarantee you will develop expertise in mission planning and drone flying, without previous experience or if you're already experienced. While this tool is specifically designed to simulate our drone hardware, it can also serve as a highly realistic proxy for any multi-rotor drone.
For many years, challenging logistics and regulatory hurdles kept many teams from adopting drone technology. Are those challenges and hurdles significantly different in 2025? Or that much less than they were in the past?
I agree with your statement, though with some distinctions. While regulation in the US appears to have brought greater clarity and expanded possibilities, the new EASA regulations in Europe are significantly more complex, for many users even confusing. This complexity has without doubt slowed the adoption of drone strategies across Europe. In some cases, even NAAs (National Aviation Authorities) struggle to maintain a clear overview of the entire regulatory framework. How, then, can a typical drone operator—who is unlikely to be experienced in interpreting regulatory documents—find their way through this labyrinth of rules?
As a manufacturer, AIR6 Systems has intentionally refrained from betting on the logistics sector only, precisely due to this regulatory complexity. However, this does not mean we are neglecting the sector. On the contrary, we are conducting extensive R&D to prepare our product for future opportunities. We also observe an increasing interest in drone logistics research among end-users, reflecting the sector’s potential. There is no doubt that drone logistics could become a major sub-sector of the industry, if not the largest.
For now, we focus on logistics that make clear economic sense, particularly in emergency medical applications. Our DrUBER R&D project exemplifies this approach, as we work to establish a network of medical emergency drone deliveries—initially in Essex (UK)—while also exploring alpine rescue logistics as a key area of focus.
What advice would you have for someone who thinks your solution could be a fit but isn't sure how to best explore what adoption could look like for them or their workflow?
At AIR6 Systems, we have been committed to developing industrial-grade solutions with a strong application focus from the very beginning. For anyone seeking a high-performance drone as a critical tool to streamline workflows—particularly those preferring a non-Chinese product—AIR6 Systems is the ideal choice. Our drones feature an open-architecture design, allowing for adaptability, customization, and upgrades over time to meet evolving needs. They deliver best-in-class performance, including flight times of up to 60 minutes and payload capacities of up to 10 kg (20 lbs), ideally for BVLOS use cases.
At the smaller end of our product range, we specialize in tactical reconnaissance, monitoring, and perimeter protection. For these applications, we have developed exceptionally lightweight solutions tailored for use in urban environments. Additionally, we also provide our customers with extensive training, comprehensive technical support, and access to the fully integrated digital twin simulation tool, ensuring they maximize the value and efficiency of their drone systems.
Watch a replay of the AirborneSIM webinar or connect with the AIR6 Systems team at XPONENTIAL Europe, taking place February 18-20.
Comments